Top 10 Work Comp Claim Stoppers
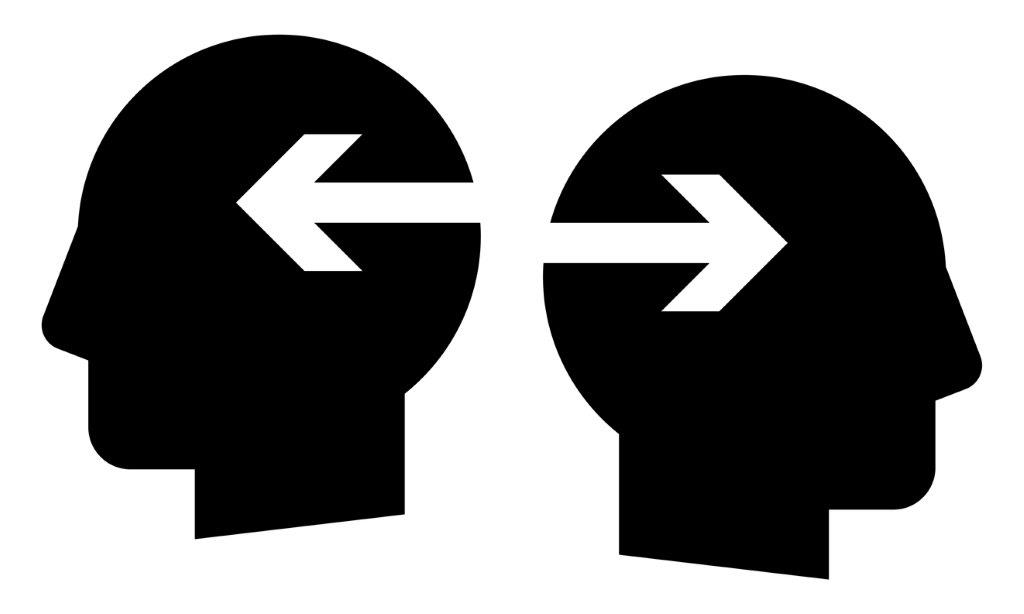
How to apply existing success energy to stop work comp claims.
Organizations that master safety leadership save time and maximize profit. The strategy is to take existing organizational success energy and apply it to stop work comp claims.
Here’s a rapid fire list of some of the most effective strategies to stop (or reduce) work comp claims.
1. Get inside their heads – What does the team believe about injuries, accidents, and the system supporting them. We need to know whether what they believe is accurate and whether it’s aligned with what it takes to stop claims.
2. “Zero Claims” goal – Accidents don’t just happen. Every process, every job has a way of being done safely. Everyone’s goal must be zero injuries. We need to know, without a doubt, that every team member knows how to do the job 100% safely.
3. Set a W.I.N culture – Every company has its own culture. The way things are handled in an organization determines the company culture. It’s the processes, systems, behaviors, and beliefs that are considered “normal” and out of which decisions are made and results are generated. To stop work comp claims, you have to change what is normal in the organization. It’s what we call W.I.N. “What Is Normal”. And all team members must be aligned…that means having everyone involved in making the changes required to stop claims.
4. Assign safety roles – Management’s role in stopping claims is to actively demonstrate a strong commitment to safety. The message has to come loud and clear from the very top. The supervisors and managers provide safety leadership. The qualified safety person (safety manager) provides proactive communication and enforcement. Team members (employees) must know how to do their job 100% safely.
5. Train manager leaders – Middle level managers and supervisors are the key to eliminating work comp claims because they are the closest to the people having the claims. Make sure people love working for your managers. Once managers learn to lead in safety and in enterprise value, the incidence of work comp claims dwindles and profitability soars.
6. Coach team members – Just like great athletes, team members need both training and coaching. Training is skills based. It fills a skills gap. Coaching is a personalized learning experience building on the skills a person has. The key is in getting effective coaching done by managers. To stop work comp claims, we train for safety skills and coach so the behaviors become “normal”.
7. Treat injuries appropriately – For best results, it’s important to guide injured workers to the appropriate level of care…is it first aid, an occupational medical clinic, an emergency room, or a 911 call? Explain to team members, especially new team members, that multi-layered care is provided…care that is customized if they are injured on the job.
8. Get them back to work – Maintain an active return-to-work program. Identify modified duty opportunities to help support anyone who does become injured on the job and requires temporary, limited, or light duty work while recovering. Keep a list of modified duty opportunities throughout the organization. The goal is for team members to become “well and working” as soon as possible.
9. Invest in an effective incentive plan – Incentive plans that reward people for not making work comp claims when they are injured or that target an injured worker that has a lost time claim as a bad guy will ultimately cause work comp costs (premiums) to go up. They are also frowned upon by OSHA. A great incentive plan promotes proactive safety awareness, rewards safety compliance and recognizes safety success.
10. Act fast – Make sure the work comp technology is delivering “instant” guidance. The ability to monitor results in real time is critical. The platform should not only proactively report on progress, but also eliminate redundant data entry. This means work comp data that is submitted on a claim, simultaneously completes the OSHA logs, trending reports, and satisfies OSHA’s electronic filing requirements.